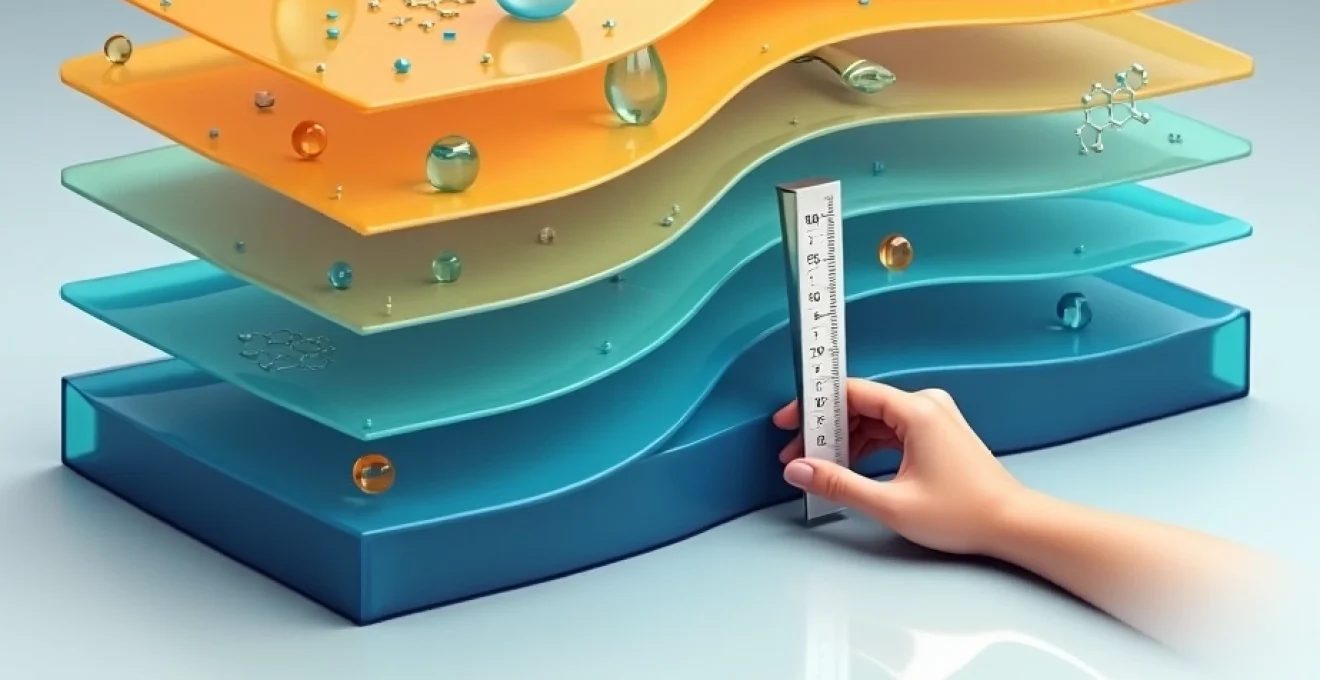
La résine époxy est un matériau polyvalent largement utilisé dans divers domaines, de la construction à l'artisanat. Son application en plusieurs couches est souvent nécessaire pour obtenir des résultats optimaux. Cependant, déterminer le temps d'attente idéal entre chaque couche est crucial pour garantir une adhérence parfaite et éviter les problèmes potentiels. Ce délai dépend de nombreux facteurs, notamment la composition chimique de la résine, les conditions environnementales et les techniques d'application. Comprendre ces éléments est essentiel pour réussir vos projets en résine époxy et obtenir des finitions durables et esthétiques.
Chimie des résines époxy et temps de polymérisation
La résine époxy est un polymère thermodurcissable composé de deux éléments principaux : la résine de base et le durcisseur. Lorsque ces composants sont mélangés, une réaction chimique appelée polymérisation se produit. Cette réaction transforme le mélange liquide en un solide dur et résistant. Le temps nécessaire à cette transformation complète est appelé temps de polymérisation.
Le processus de polymérisation se déroule en plusieurs étapes. Initialement, le mélange reste liquide et peut être travaillé. Cette période est appelée pot life
ou durée de vie en pot. Ensuite, la résine commence à gélifier, devenant de plus en plus visqueuse jusqu'à atteindre un état solide mais encore malléable. Enfin, elle durcit complètement pour atteindre ses propriétés mécaniques finales.
La compréhension de ce processus est fondamentale pour déterminer le moment optimal pour appliquer une nouvelle couche. Appliquer trop tôt peut perturber la polymérisation en cours, tandis qu'attendre trop longtemps peut compromettre l'adhérence entre les couches.
La maîtrise du temps de polymérisation est la clé d'une application réussie de résine époxy en plusieurs couches.
Facteurs influençant le temps d'attente entre les couches
Plusieurs facteurs peuvent affecter significativement le temps d'attente nécessaire entre les couches de résine époxy. Ces éléments doivent être pris en compte pour assurer une application optimale et des résultats durables.
Température ambiante et son impact sur la réticulation
La température joue un rôle crucial dans le processus de polymérisation de la résine époxy. En général, des températures plus élevées accélèrent la réaction chimique, réduisant ainsi le temps de prise. Inversement, des températures basses ralentissent le processus. Pour la plupart des résines époxy, la température idéale d'application se situe entre 20°C et 25°C.
Il est important de noter que des variations de température importantes pendant le processus de durcissement peuvent affecter les propriétés finales de la résine. Par exemple, une augmentation soudaine de la température peut entraîner un durcissement trop rapide de la surface, empêchant une polymérisation complète à l'intérieur.
Humidité relative et son effet sur le durcissement
L'humidité relative de l'environnement peut également influencer le temps de durcissement de la résine époxy. Une humidité élevée peut ralentir le processus de polymérisation et, dans certains cas, affecter les propriétés finales du matériau. Certaines résines époxy sont particulièrement sensibles à l'humidité et peuvent développer un voile blanchâtre à la surface si elles sont exposées à des conditions trop humides pendant le durcissement.
Il est recommandé de travailler dans un environnement où l'humidité relative est inférieure à 70%. L'utilisation d'un déshumidificateur peut être nécessaire dans certaines situations pour maintenir des conditions optimales.
Épaisseur des couches et temps de séchage
L'épaisseur de chaque couche de résine époxy a un impact direct sur le temps de séchage. Des couches plus épaisses nécessitent généralement plus de temps pour polymériser complètement. Cela s'explique par le fait que la réaction exothermique (qui produit de la chaleur) au cœur de la couche peut être plus intense, entraînant parfois des problèmes comme la formation de bulles ou un jaunissement prématuré.
Pour éviter ces problèmes, il est souvent préférable d'appliquer plusieurs couches fines plutôt qu'une seule couche épaisse. Chaque couche aura ainsi le temps de durcir correctement avant l'application de la suivante.
Type de durcisseur utilisé (amine, anhydride, phénol)
Le choix du durcisseur a une influence significative sur le temps de polymérisation et les propriétés finales de la résine époxy. Les trois types principaux de durcisseurs sont :
- Amines : Offrent un durcissement rapide mais peuvent être sensibles à l'humidité.
- Anhydrides : Procurent un durcissement plus lent mais une meilleure résistance thermique.
- Phénols : Fournissent une excellente résistance chimique mais nécessitent souvent des températures élevées pour durcir.
Le choix du durcisseur dépendra de l'application spécifique et des conditions de travail. Par exemple, pour des projets nécessitant un temps de travail plus long, un durcisseur à base d'anhydride pourrait être préférable.
Techniques de mesure du temps de prise optimal
Pour déterminer avec précision le moment idéal pour appliquer une nouvelle couche de résine époxy, plusieurs techniques de mesure peuvent être employées. Ces méthodes permettent d'évaluer objectivement l'état de polymérisation de la couche précédente.
Test de dureté shore D pour évaluer la polymérisation
Le test de dureté Shore D est une méthode couramment utilisée pour évaluer le degré de durcissement de la résine époxy. Il mesure la résistance du matériau à la pénétration d'une pointe standardisée. Plus la valeur Shore D est élevée, plus le matériau est dur et donc polymérisé.
Pour utiliser cette technique, un duromètre Shore D est nécessaire. La mesure est généralement effectuée à différents points de la surface pour obtenir une moyenne représentative. Une valeur Shore D typique pour une résine époxy complètement durcie se situe entre 70 et 85.
Un test de dureté Shore D supérieur à 75 indique généralement que la couche de résine époxy est suffisamment durcie pour recevoir une nouvelle application.
Utilisation d'un hygromètre pour contrôler l'humidité
L'utilisation d'un hygromètre est cruciale pour surveiller l'humidité relative de l'environnement de travail. Cet instrument mesure le taux d'humidité dans l'air, un facteur qui peut significativement affecter le temps de durcissement de la résine époxy.
Pour des résultats optimaux, l'humidité relative devrait idéalement se situer entre 40% et 60% pendant l'application et le durcissement de la résine. Un taux d'humidité trop élevé peut ralentir le processus de polymérisation et potentiellement affecter la qualité de la finition.
Méthode du gel-timer pour déterminer le temps de travail
La méthode du gel-timer est utilisée pour déterminer le pot life
ou temps de travail de la résine époxy. Cette technique consiste à mesurer le temps nécessaire pour qu'un petit échantillon de résine mélangée atteigne un état de gel.
Pour réaliser ce test, un petit échantillon du mélange résine/durcisseur est placé dans un récipient et régulièrement testé avec un bâtonnet. Le moment où le mélange devient trop visqueux pour couler librement marque la fin du temps de travail. Cette information est précieuse pour planifier l'application des couches successives.
Intervalles recommandés selon les types de résines
Les intervalles d'attente entre les couches de résine époxy varient considérablement selon le type de résine utilisé. Chaque formulation a ses propres caractéristiques de durcissement et exigences spécifiques.
Résines époxy à prise rapide (west system 105/205)
Les résines époxy à prise rapide, comme le système West System 105/205, sont conçues pour durcir rapidement, permettant une application plus fréquente des couches. Typiquement, ces résines permettent l'application d'une nouvelle couche après 4 à 6 heures de durcissement à température ambiante (20-25°C).
Ces systèmes sont particulièrement adaptés pour les projets nécessitant une progression rapide ou lorsque les conditions environnementales sont contrôlées. Cependant, il est crucial de respecter scrupuleusement les temps recommandés pour éviter tout problème d'adhérence entre les couches.
Résines époxy à prise lente pour coulées épaisses (ArtResin)
Les résines époxy à prise lente, telles que ArtResin, sont formulées pour des applications nécessitant des couches plus épaisses ou un temps de travail prolongé. Ces résines peuvent nécessiter un temps d'attente de 24 à 72 heures entre les couches, selon l'épaisseur et les conditions ambiantes.
L'avantage de ces résines est qu'elles permettent une meilleure dissipation de la chaleur générée pendant la polymérisation, réduisant ainsi les risques de formation de bulles ou de jaunissement dans les coulées épaisses. Elles offrent également plus de temps pour travailler les détails ou incorporer des éléments décoratifs.
Résines époxy UV pour applications spécifiques
Les résines époxy UV représentent une catégorie spéciale conçue pour durcir rapidement sous l'effet de la lumière ultraviolette. Ces résines peuvent atteindre un état de durcissement suffisant pour l'application d'une nouvelle couche en quelques minutes d'exposition aux UV.
Bien que très pratiques pour certaines applications spécifiques, comme la création de bijoux ou la réparation rapide, ces résines nécessitent un équipement spécial (lampe UV) et sont généralement limitées à des applications en couches fines. Leur utilisation demande une attention particulière pour éviter un durcissement prématuré avant la fin de l'application.
Conséquences d'une attente inadéquate entre les couches
Le non-respect des temps d'attente recommandés entre les couches de résine époxy peut entraîner diverses complications, compromettant la qualité et la durabilité du projet final. Il est essentiel de comprendre ces risques pour apprécier l'importance d'une patience appropriée dans le processus d'application.
Problèmes d'adhérence et délamination
L'un des problèmes les plus critiques résultant d'une attente insuffisante entre les couches est la mauvaise adhérence. Si une nouvelle couche est appliquée avant que la précédente ne soit suffisamment polymérisée, la liaison chimique entre les deux peut être compromise. Cela peut conduire à une délamination, où les couches se séparent au fil du temps, ruinant l'intégrité structurelle et l'apparence de l'ouvrage.
Dans certains cas, la délamination peut ne pas être immédiatement visible, mais se manifester ultérieurement sous l'effet de contraintes mécaniques ou de variations de température. Ce phénomène est particulièrement problématique dans les applications structurelles ou exposées à des conditions environnementales difficiles.
Formation de bulles et imperfections de surface
Une autre conséquence fréquente d'une attente inadéquate est la formation de bulles ou d'autres imperfections de surface. Lorsqu'une nouvelle couche est appliquée trop tôt, les solvants ou les sous-produits de la réaction de polymérisation de la couche inférieure peuvent se retrouver piégés. En essayant de s'échapper, ils créent des bulles ou des cratères dans la surface.
Ces défauts non seulement compromettent l'esthétique du projet, mais peuvent également affecter les propriétés mécaniques et la durabilité de la finition. Dans certains cas, ces imperfections peuvent nécessiter un ponçage et une nouvelle application, augmentant considérablement le temps et le coût du projet.
Jaunissement prématuré et perte de transparence
Le jaunissement prématuré et la perte de transparence sont des problèmes particulièrement préoccupants pour les applications où l'aspect visuel est primordial. Une polymérisation incorrecte due à une application trop rapide des couches peut accélérer le processus de jaunissement, un phénomène naturel des résines époxy mais généralement lent dans des conditions normales.
De plus, une réaction chimique incomplète entre les couches peut entraîner une opacification ou une perte de clarté, particulièrement visible dans les projets nécessitant une finition cristalline. Ce problème est souvent irréversible et peut nécessiter le retrait complet et la réapplication de la résine.
Une patience adéquate entre les couches de résine époxy n'est pas seulement une question de temps, mais un investissement dans la qualité et la longévité du projet.
Optimisation du processus multicouche en résine époxy
Pour maximiser les chances de réussite lors de l'application de multiples couches de résine époxy, il est essentiel d'optimiser chaque étape du processus. Cette optimisation implique une préparation méticuleuse, des techniques d'application précises et parfois l'utilisation d'additifs spécialisés.
Préparation de surface entre les couches (ponçage, nettoyage)
La préparation de la surface entre chaque couche est une étape cruciale pour assurer une adhérence optimale. Même si le temps d'attente recommandé a été respecté, un léger ponçage de la surface peut grandement améliorer l'accroche de la couche suivante.
Utilisez un papier de verre à grain fin (220-400) pour créer une légère rugosité sur la surface durcie. Cette opération, appelée ponçage de liaison, augmente la surface de contact et favorise une meilleure adhérence mécanique entre les couches.
Après le ponçage, il est essentiel de nettoyer soigneusement la surface pour éliminer toute poussière ou résidu. Utilisez un chiffon non pelucheux imbibé d'alcool isopropylique ou d'un solvant recommandé par le fabricant de la résine. Un nettoyage inadéquat peut laisser des contaminants qui compromettront l'adhérence de la nouvelle couche.
Techniques d'application pour une adhérence maximale
L'application de chaque nouvelle couche de résine époxy doit être effectuée avec soin pour assurer une adhérence optimale. Une technique couramment utilisée est la méthode de l'application humide sur humide. Cette approche consiste à appliquer la nouvelle couche lorsque la précédente est encore légèrement collante au toucher, mais suffisamment durcie pour ne pas se mélanger.
Lors de l'application, veillez à maintenir une épaisseur uniforme. Utilisez un rouleau à poils courts ou une spatule crantée pour répartir la résine de manière homogène. Pour les surfaces verticales ou courbes, envisagez l'utilisation d'une résine thixotrope qui ne coulera pas pendant le durcissement.
Une autre technique efficace est l'application par pulvérisation, particulièrement utile pour les grandes surfaces ou les formes complexes. Cette méthode permet une couverture uniforme et peut réduire le risque de piéger des bulles d'air entre les couches.
Utilisation d'additifs pour moduler le temps de prise
Des additifs spécialisés peuvent être incorporés à la résine époxy pour ajuster ses propriétés de durcissement et optimiser le processus multicouche. Ces additifs offrent une flexibilité supplémentaire dans la gestion du temps entre les applications.
Les accélérateurs sont des additifs qui réduisent le temps de durcissement de la résine. Ils sont particulièrement utiles dans des environnements froids ou lorsqu'un durcissement rapide est nécessaire. Cependant, leur utilisation doit être soigneusement contrôlée pour éviter un durcissement trop rapide qui pourrait compromettre l'adhérence entre les couches.
À l'inverse, les retardateurs prolongent le temps de travail de la résine. Ils sont bénéfiques dans des conditions chaudes ou pour des projets complexes nécessitant plus de temps de manipulation. Les retardateurs peuvent également aider à réduire la génération de chaleur dans les coulées épaisses, minimisant ainsi le risque de fissures ou de jaunissement.
L'utilisation judicieuse d'additifs peut transformer un processus d'application multicouche complexe en une opération fluide et maîtrisée.
Enfin, certains additifs peuvent améliorer les propriétés de mouillage de la résine, favorisant une meilleure adhérence entre les couches. Ces agents de mouillage réduisent la tension superficielle de la résine, permettant une couverture plus uniforme et une pénétration améliorée dans les micropores de la surface précédente.
En combinant ces techniques de préparation, d'application et l'utilisation stratégique d'additifs, vous pouvez optimiser significativement le processus d'application multicouche de résine époxy. Cette approche méthodique garantit non seulement une adhérence supérieure entre les couches, mais aussi une finition de haute qualité qui résistera à l'épreuve du temps.